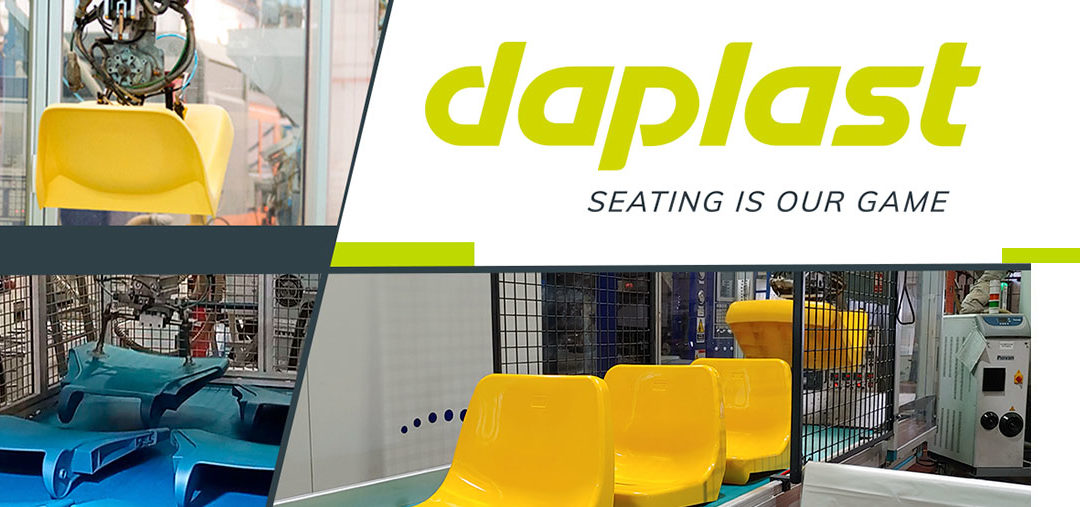
What difference does it make? Injection moulded seats vs. blow moulded seats
Both technologies are the most used to produce stadium seating. A wide variety of stadium seats can be found on the market that are manufactured using one of these two processes.
Essentially, in injection moulding, the material is melted and introduced in the mould through one or more orifices at very high pressures.
Whereas in blow moulding production, the material is semi-melted and inserted as a shape of semi-molten plastic sleeve or parison into a mould. Once the mould is closed, air is blown with pressure to form a moulded hollow body in the shape of the mould.
But which technology is the most suitable for each project? Are there differences in the stadium seats obtained, and which production system makes it possible to create more original stadium seats designs?
Let’s review the most important characteristics to choose the best stadium seat for each project:
- Design is an important factor to consider depending on the requirements of each project. Blow moulded stadium seats allow designs with more volume or hollow geometries. However, injection moulded seats have more limitations in terms of geometry and thickness. In their favour, the injection moulding process allows greater definition, precision, and detail in the pieces. The appearance of the surface of the seat or backrest is better finished because the piece copies the mould surface with great precision.
- Mechanical strength depends on the geometry of the piece rather than the process. Although there are more and higher quality materials available for injection moulding than those available for blow moulding.
- Cost-effectiveness: there are differences between investment in machinery and investment in moulds. On the one hand, the required investment in blow moulding machinery is higher than in injection moulding, as injection moulding machinery is produced in large series, which saves on costs.On the contrary, blow moulds are more economic than injection moulds, because blow moulds work at lower pressures and are softer and easier to produce than injection moulds.How does this impact on a seating project? When we are designing a new seat or backrest for a specific project, factors such as seat design (geometry) and the volume of production must be considered. Depending on the customer’s requirements, we will choose the most suitable manufacturing technology, from both technical and economical points of view.
- Delivery times: Injection moulding production times are faster and the final finish requires less manipulation than in the case of blow moulding. This translates into higher availability for short series, and better lead times in the case of injection moulded seat production.
Avatar Seating manufactured by inyection moulding.
Sittem seats manufactured by blow moulding.
Which seats are the best, those produced by injection moulding or those produced by blow moulding? How does the production system affect the result?
In conclusion, they are different processes, each one with its own advantages or weaknesses.
There is no one process that is better than another. It depends on the design of each part or component of the seat, the choice of one system or the other.
Blow moulding is a suitable process to obtain a seat or backrest formed from a hollow part, offering different opportunities in aesthetics, volume and geometry of the product.
For structural parts of the seat, the injection moulding process is better, allowing the use of technical materials and precise and defined geometries.
The combination of the two technologies offers more opportunities in terms of product design. Daplast has both technologies and is betting on this combination.